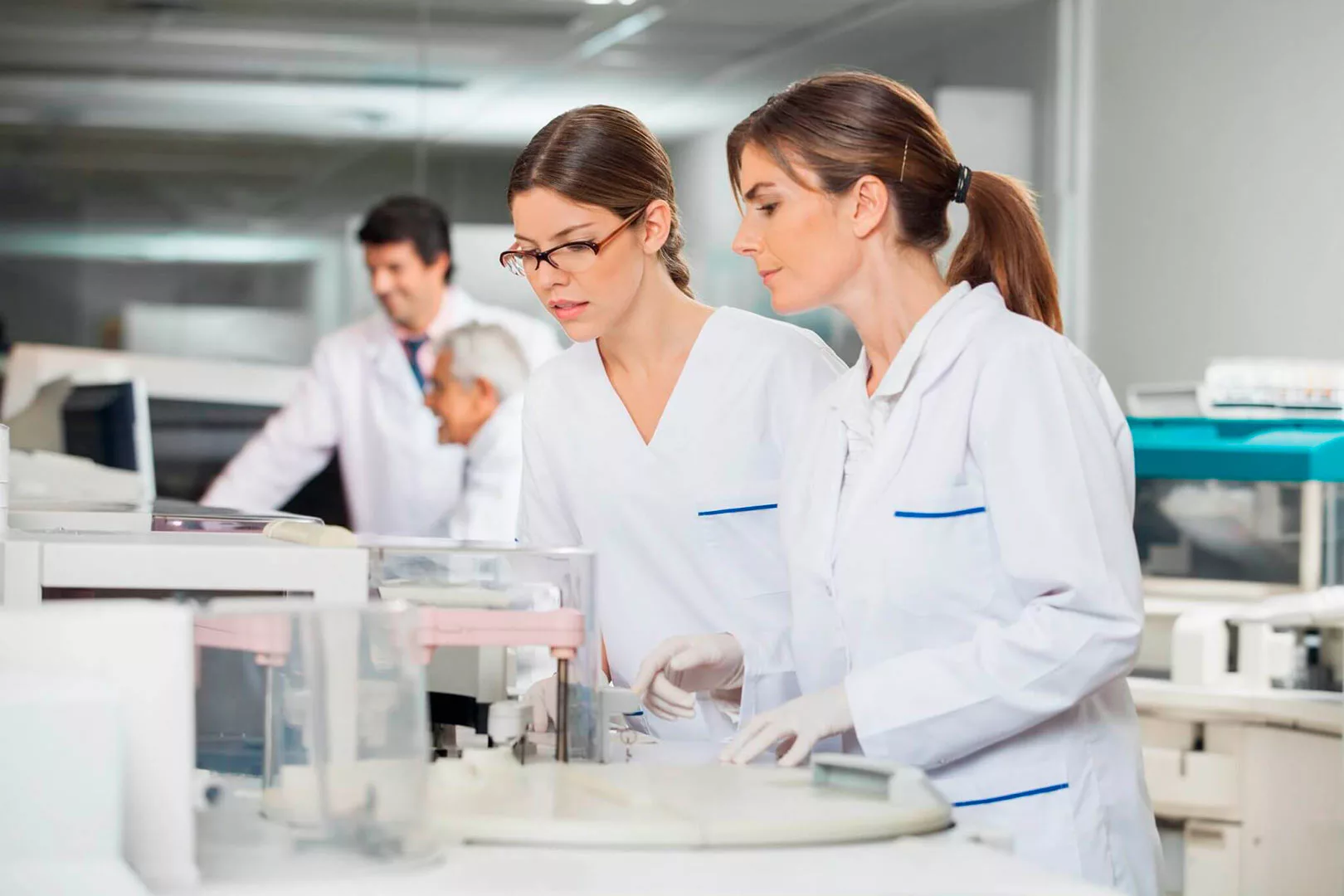
Our Quality
Our Quality
The quality of workwear fabrics is formed at every stage of their manufacture, from spinning raw fibres into yarn to finishing a woven fabric..
Yarn production, weaving a greige fabric, dyeing (adding colour) and adding finishes (such as water-repellent or oil-resistant properties) – all these major steps are very complex processes.
Therefore, the task of improving quality can only be solved by a careful and regular control system of each stage of production.
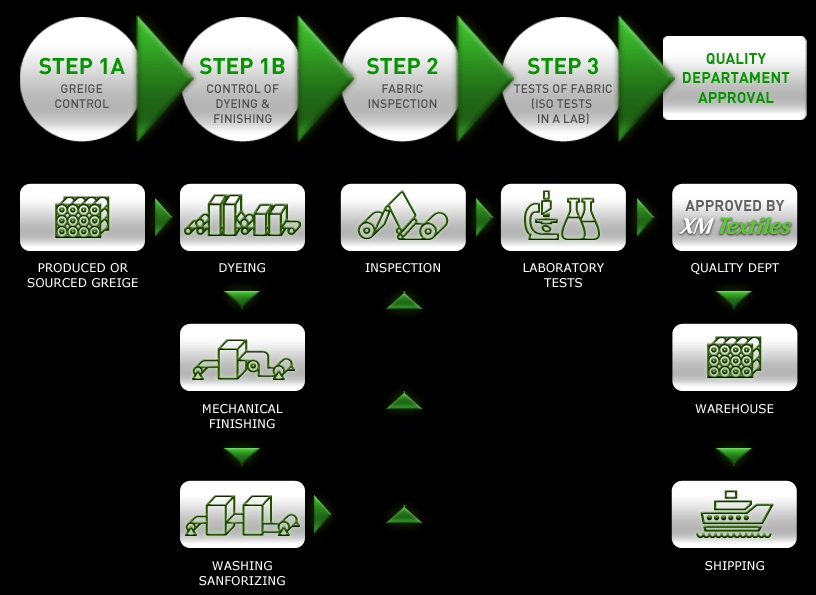
XM Textiles™ has developed and used the following three stages quality control system for workwear fabrics:
The 1-st stage includes control of early steps of workwear fabric production, namely:
1.1 Greige fabric examination
1.2 Inspection the colour of the fabric after dyeing and its additional finishes (like WR, Oil-proof etc.)
At the 2-nd stage, XM Textiles™ examines the finished workwear fabric. According to common standards, our experts inspect not less than 10% of total production lots.
XM Textiles applies the “Ten Points” method of fabric quality control (QC), which is similar to the American system “Four Points”. Our QC-managers assigns a certain amount of points to each defect according to its kind and size. After that, we calculate the total amount of points per roll and conclude its quality.
At the 3-d stage samples of workwear fabric are tested in our lab according to ISO standards. We have modern equipment and use it to test the following parameters:
Shrinkage
Colour fastness to washing, wet and dry rubbing
Tearing strength
Tensile strength
Colour matching
Water repellency properties (for PU-coating or WR-finish for workwear fabrics for raincoats etc.)
Other parameters we test in internationally certified labs (STR, SGS, AITEX(Spain), BTTG (UK) etc.):
1. Colour fastness to light
2. Formaldehyde content
3. AZO content
4. Shrinkage of workwear fabric for industrial washes (ISO 15797) etc.
Beside this Quality Control System (QCS), in 2015 our workwear fabrics have been certified to Oekotex Standard 100 by Testex AG (Switzerland). Since then, Testex AG has been testing our fabrics and renewing Oekotex-100 certificate every year. You can look at our last Oekotex certificate on this page.
We are focused on delivering workwear fabric to our clients, which is safe to wear and free from harmful substances. We also think that the OEKO-TEX® certificate is a must-have for all eco-conscious workwear manufactures.
Buy XM Textiles™ OEKO-TEX® workwear fabrics to make workwear healthier!
The quality of workwear fabrics depends on how all stages of production starting from manufacturing of yarn for grey cloth up to the finishing. Therefore quality control and enhancement can be accomplished only by setting up of thorough and successful Quality Management System (QMS) which supervises all the manufacturing processes.
Testing criterions used by XM Textiles are based on ISO standards (for example, shrinkage – ISO 6330-2000, colour fastness to rubbing – ISO 105 X12-2001, etc.)
XM Textiles QMS consist of the following three main stages of quality control:
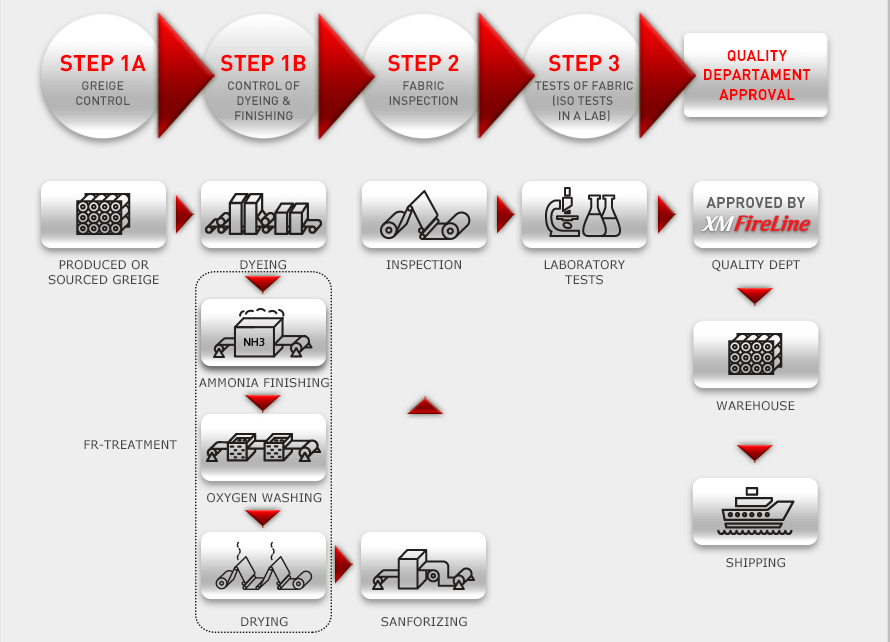
The first stage includes testing the fabric at the place of production, namely:
– Grey examination
– Controlling of the process of preparing grey cloth for dyeing and dyeing itself
– Inspecting adherence of finishing technology
At the second stage XM Textiles examines the finished products. According to common standards our experts inspect not less than 10% of total order amount. XM Textiles applies “Ten Points” method of fabric quality control which is created on the basis of American system “Four Points”. Current system assigns a certain amount of points to each defect according to its location (warp wise or weft wise) and size. After that we can calculate total amount of points per roll and make a conclusion about its quality.
At third stage samples are sent to our laboratory to provide final examination according to ISO standards as well as to confirm the shipment of present order. Under laboratory conditions we test shrinkage, color fastness to washing, wet and dry rubbing, tearing and tensile strength, color matching and PU-coating or WR-finish for fabrics which obtain these characteristics. When impossible to make examination in our laboratory (for example, for color fastness to light or formaldehyde content), samples are inspected in STR and SGS laboratories, which results are accepted worldwide.
FIRE RESISTANT TECHNOLOGY THPC-processing for flame-retardant fabrics XM FIRELINE.
XM FireLine – flame retardant fabrics manufacturer
Our company produces flame retardant fabrics under the brand XM FireLine for the manufacturing of protective and fr clothing. These fabrics are treated with flame retardant THPC in compliance with all technological standards, ensuring a high level of safety of the work wear.
What is THPC?
The basis of the fabrics treatment process is a chemical THPC C4H12ClO4P (tetra (hydroxymethyl) phosphonium chloride) internationally recognized as one of the best fire retardants for processing cotton and mixed (the CVC) fabrics. The THPC composition treated fabric using a special process. Thus the preparation uniformly coats the fabric fibers and deeply penetrates, being fixed in their structure, whereby the fabric becomes fire resistance property. Flame retardant properties are maintained during long-term storage as well as laundry and dry cleaning.
XM FireLine company carefully monitors compliance with all processes requirements, to ensure the high flame retardant proprieties of the fabrics (fabrics are not glowing; the flame does not spread outside the charred area).
THPC – fabric processing technology
After the stage of fabric dyeing XM FireLine fabrics pass the following stages of the process to make it flame retardant.
1. The fabric is passed through a container with a chemical solution THPC.
2. The fabric is dried on drying machine.
3. Next step, the fabric passes through a sealed tank where ammonia gas under the influence of the polymerization process occurs.
4. The fabric passes through a bath with an oxidizing agent, where the surplus ammonia neutralized.
5. The fabric passes through a series of wash baths, where residues are removed.
6. The fabric final drying stage and it is ready for use.
XM FireLine flame retardant fabrics pass a visual inspection and check for the key parameters.
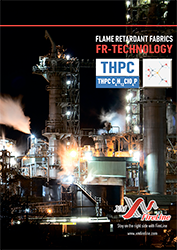
Download FR-Technology Leaflet

XM FireLine flame retardant fabrics characteristics
Fabric XM FireLine, held at THPC processing technology, has the following properties:
– no residual heating and melting;
– dual decay time after stopping of the flame is not more than 2 seconds;
– molten metal splash protection;
High durability guarantees maintenance of flame retardant fabrics properties for a long fabric lifetime:
* maintaining of high mechanical properties of the original fabric;
* maintaining of flame retardant properties after 100 washes;
To maintain the flame retardant properties of the XM FireLine fabrics you must always follow the care instructions (see. Annex 1)
XM FireLine fabrics Applications
Nowadays the flame retardant fabrics are widely used for protective work wear manufacturing around the world. This is due to the fact that the requirements of international standards for the safety of workers become stricter. XM FireLine follows the world trends and every year try to develop new variants of fabrics for protection not only from fire and flame but also from electric arc, static electricity, acids, alkalis and other risks.
XM FireLine fabrics recommended for the producing of protective and flame retardant work wear at work associated with short-term exposure to an open flame, heat radiation (metallurgists, firemen), and the possibility of welding sparks and molten metal splash, high heat or electric arc.
P.S. Be sure to consult with a technician for the safety of your production, to choose fireproof fabric XM FireLine appropriate level of protection.
Annex 1
Flame Retardant Fabric Care Requirements
XM FireLine flame retardant fabrics domestic wash 600C and Industry wash at 750C required.
Soft water is recommended. Hard water precipitates soaps and contains calcium and magnesium salts. These can build up on the fiber surfaces, coating the fabric and masking luminescent or FR properties.
Do not use natural soaps (anionic or tallow soap).
Magnesium and calcium deposits can be removed in a commercial laundry with acetic acid during followed by rinsing with the alkaline neutralization.
Do not use chlorine-based bleaches because they are chemically weaken polymeric compounds that provide flame retardant properties of the fabric.
Annex 2
ISO 11612:2008 Protective clothing – Clothing to protect against heat and flame
ISO 11612:2008 specifies performance requirements for garments made from flexible materials, which are designed to protect the wearer’s body, except the hands, from heat and/or flame. For protection of the wearer’s head and feet, the only items of protective clothing falling within the scope of this International Standard are gaiters, hoods and overboots. However, concerning hoods, requirements for visors and respiratory equipment are not given.
ISO 11611:2015 Protective clothing for use in welding and allied processes
ISO 11611:2015 specifies minimum basic safety requirements and test methods for protective clothing including hoods, aprons, sleeves, and gaiters that are designed to protect the wearer’s body including head (hoods) and feet (gaiters) and that are to be worn during welding and allied processes with comparable risks. For the protection of the wearer’s head and feet, this International Standard is only applicable to hoods and gaiters. This International Standard does not cover requirements for feet, hand, face, and/or eye protectors.
This type of protective clothing is intended to protect the wearer against spatter (small splashes of molten metal), short contact time with flame, radiant heat from an electric arc used for welding and allied processes, and minimizes the possibility of electrical shock by short-term, accidental contact with live electrical conductors at voltages up to approximately 100 V d. c. in normal conditions of welding. Sweat, soiling, or other contaminants can affect the level of protection provided against short-term accidental contact with live electric conductors at these voltages.
REFLECTIVE TECHNOLOGY
XM SilverLine™ designs and manufactures reflective tapes for High Visibility workwear, Protective clothing and Firefighters uniform. We have 15 years experience of work with reflective materials and sell them in 51 countries. All our FR-tapes resist 50/100 wash cycles and certified to EN 469 and EN 20471. We test every production lot to deliver you 100% quality.
When creating reflective tapes, we do count every detail and trims to comply with main European and American standards. You can look at all our certificates on our web-site. We have tested and certified our tapes & trims to the following safety standards: EN 20471, EN 469, NFPA 2112
GLASS BEADS TECHNOLOGY
Each glass bead works as follows: An incoming light beam refracts as it passes through the front surface of the glass bead and reflected off a mirrored surface behind the bead again. The beam then passes back through the front surface, and returns toward the light sources.
Reflective tapes using glass beads are more affordable. For a manufacturer in need of a large quantity of reflective tape to produce high visibility safety gear, glass bead technology is simpler to manufacturer – thus a reduced cost and less of a hit on inventory budget controls.
Engineer Grade Glass Bead Reflective Tape
Engineer grade reflective starts with a carrier film that is metalized on the top. Glass beads are applied to this layer so that about 50 percent of the bead is embedded in the metalized layer. This gives the beads their reflective properties. Then a layer of either acrylic or polyester is applied over the top. This layer can be clear to made white reflective tape or it can be colored to create the different color reflective tapes. A layer of adhesive is then applied to the bottom of the tape and a release liner is applied to that layer. It is rolled up, slit to width and then sold. Note – an acrylic layered film will not stretch and a polyester layered film will. Because of the heat used in the manufacturing process engineer grade films end up being a single layer so they will not delaminate.
High Intensity Glass Bead Reflective Tape
High intensity type 3 reflective tape is made in layers also. The first layer if one that has a grid built into it. Normally a honeycomb type pattern. This pattern is what will hold the glass beads so that they are in separate cells. The glass beads are bonded to the bottom of this cell then a layer of acrylic or polyester is applied over the top of the cell so that there is a small air space above the beads. (high index beads) This layer can be clear or a color. Then a layer of adhesive and a release liner are applied to the bottom of the tape. Note – an acrylic layered film will not stretch and a polyester layered film will. Although the layers in high intensity are bonded together, they can delaminate.
MICRO-PRISMATIC TECHONLOGY
Microprismatic Technology incorporates retro-reflective microscopic prisms formed on a polymeric film to create a bright reflective appearance on garments and accessories.
Prismatic reflective tape is more efficient, returning about 80% of the light to the source as opposed to the 30% offered by glass bead designs. This makes prismatic reflective tape brighter. While the other type uses glass beads, this type of reflective tape uses man-made prisms designed with hard angle mirrors. Because of this, the light is more focused and can travel a much greater distance without dimming.
The microprism’s economical use of surface area delivers a higher level of performance in all applications, which results in superior long distance visibility of the vehicle and greater awareness by the motoring public.
Distance plays a crucial factor in the popularity of this tape. There are many long distance requirements by ANSI and DOT at distances of 1000 feet or more.
Metalized Micro-Prismatic Reflective Tape
Metalized micro-prismatic reflective tape is made by first creating a prism array out of clear or colored acrylic or polyester (vinyl). This is the top layer. This layer provides reflectivity and returns light back to the source. A colored layer would return light back to the source but in a different color. This layer is metalized to enhance its reflectivity. Then a layer of adhesive is applied to the back and a release liner is applied. Because of the heat used in this process the layers of metalized prismatic will not delaminate. This is especially beneficial in applications such as vehicle graphics or any other application where the tape may be treated harshly. Reflexite invented prismatic reflective tape and their tapes do not delaminate.
Non Metalized Micro-Prismatic Reflective Tape
Much like metalized films, the first step in creating non metalized reflective films is to create the prism array out of acrylic or another clear resin. This will be the top layer of the film. It can be clear or colored. In order to create a whiter or a more vivid colored film, the prism layer is adhered to a grid that forms a sort of honeycomb pattern. This creates an air layer below the prisms. The surface below the air layer is white. The prism layer and the grid layer are bonded together but can come apart meaning that non metalized films can delaminate. By eliminating the metalizing of the prisms the tapes are more vivid since the color does not have to compete with the silver metalizing layer. Non metalized films are more vivid but not necessarily more reflective.
The image below shows the 4 types of reflective films. All are made in a similar way. The glass bead engineer grade film is the easiest to make and thus the least expensive. The high intensity is the next easiest and next in price.
The metalized micro-prismatic films are the most expensive to make but are the brightest and toughest of all the reflective tapes.